Ambuja Cements Limited, a prominent player in India’s cement sector and a part of the diversified Adani Group, recently conducted its earnings conference call for the third quarter of the fiscal year 2025 (Q3 FY 2025). The call offered important insights into the company’s financial results, operational highlights, and strategic plans designed to enhance its market position and promote sustainable growth.
This article presents the main points from the earnings call, providing a thorough overview of Ambuja Cements’ performance, challenges, and outlook for the future in a fluctuating market landscape.
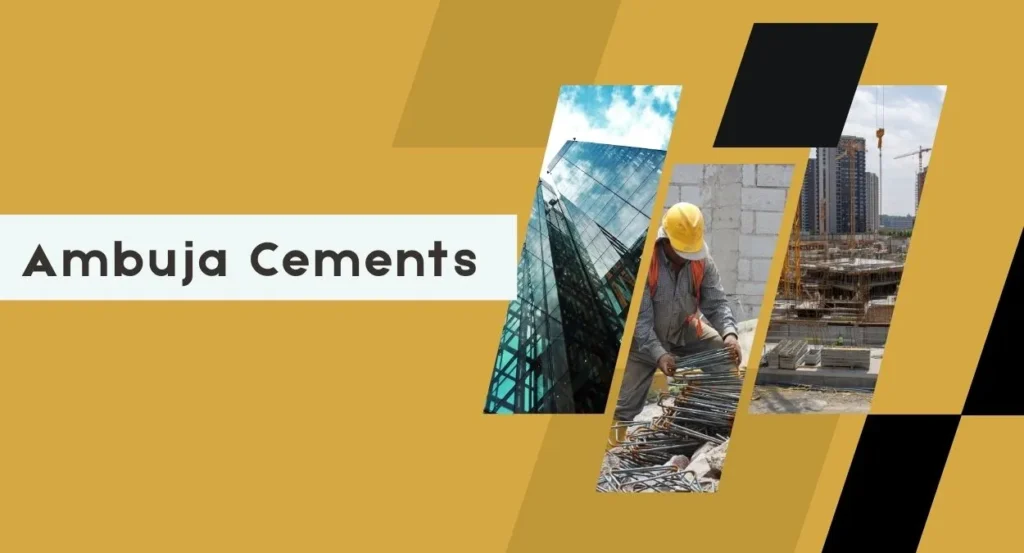
Financial Performance
Metric | Q3 FY 2025 | 9M FY 2025 | Key Notes |
---|---|---|---|
Revenue (Consolidated) | INR 9,329 crores | INR 25,156 crores | Driven by volume growth (17% YoY) and market strategies. |
Operational Cost/ton | INR 4,618 | INR 4,520 | 7% reduction in energy costs (better fuel mix, green power). |
EBITDA | INR 1,712 crores | INR 4,103 crores | Margin: 18.4% (Q3), 16.3% (9M). |
EBITDA/ton | INR 1,038 | INR 881 | Improved cost control initiatives. |
Cash & Equivalents | INR 8,755 crores | – | Strong liquidity; nil debt (AAA rating). |
Volume (Consolidated) | 16.5 million tons | – | Includes 1.4M tons from Sanghi (0.5M) & Penna (0.9M). |
Capex (9M FY25) | INR 6,200 crores | FY25 Target: ~INR 9,000 crores | Focus on capacity expansion (140MTPA by FY28). |
Key updates
- 200- megawatt solar power, the project in Gujarat, Khavda, has been commissioned in Q3 FY ’25.
- 631 million tons of new limestone reserves were secured by the company in this quarter.
- With Orient acquisition at advanced stage, the total capacity by Q4 FY ’25 to hit 104 million tons.
- The company has commissioned 8 new ready-mix plants in Q3 FY ’25 thereby reaching a milestone of 100 ready-mix plants.
Capacity Expansion & Growth Strategy
- The company has planned to expand its cement capacity to 140 million tons by FY ’28.
- With the acquisition of Orient Cement, company’s operating cement capacity will go up to 97 million tons post completion of the Orient transaction.
- The company is on course to commission its 4-million-ton clinker unit in Bhatapara in Chhattisgarh and associated grinding units of Sankrail, Farakka, both in West Bengal, and Sindri in Jharkhand by the end of this financial year.
- The grinding unit of Salai Banwa in Uttar Pradesh to be commissioned in Q1 FY ’26.
- The brownfield expansion of Bathinda grinding unit in Punjab, Marwar grinding unit in Rajasthan to be commissioned in Q2 FY ’26
- The Kalamboli unit expansion in Maharashtra and Dahej grinding unit expansion in Gujarat, Jodhpur Penna grinding unit, Krishnapatnam grinding unit to be commissioned in Q3 of FY ’26.
- Further clinker unit of 4 million tons at Maratha in Maharashtra and grinding unit at Warsaliganj in Bihar are also expected to be commissioned by the end of FY ’26, enabling the company to reach 118 million tons capacity.
- The company has also identified 14 additional grinding units for which land acquisitions and statutory approvals are under process, which shall enable the company to hit 140 million tons by FY ’28.
- For all the new facilities of 4-million-ton clinker line in Bhatapara, the overall project progress is at 78%. Expected completion is Q4 FY ’25.
- For its corresponding grinding units at Farakka and Sankrail in Bengal, the overall project progress is at 87% and 82%. Major equipment has been received at site and expected completion of these units in Q4 FY ’25.
- For the new facility of 4-million-ton clinker line at Maharashtra, Maratha, contract has been awarded to EPC vendor, 72% of major equipment ordering has been done by the EPC partner and 34% civil work has been completed. Expected completion by Q3 FY ’26.
- For the new 3-million-ton clinker line at Jodhpur, which is of Penna, 85% civil work has been completed and major equipment ordering done. Expected completion by Q3 FY ’26.
- For new facilities of 2.4 million ton grinding unit at Salai Banwa in UP, 50% civil work has been completed, and 47% delivery of major equipment has been received at the site. Expected completion by Q1 FY ’26.
- Major equipment ordering for roller press at Bathinda grinding unit, fly ash grinding and blending system at Kalamboli and grinding unit at Dahej in Gujarat has been completed and all the 3 projects are under execution.
- Contracts awarded for grinding unit at Marwar Mundwa in Rajasthan and Warsaliganj in Bihar to EPC vendor, and both projects are also under active execution.
Cost Leadership Initiatives
Green Energy Push
- 200-megawatt solar power at Khavda in Gujarat has been commissioned in Q3; targeting 1,000 MW renewable energy by FY26.
- Waste Heat Recovery (WHR) capacity to increase from 40 MW to 218 MW by March 2025 (currently at 197 MW).
- 60% of power for 140MTPA capacity to come from green sources (83% for clinker production).
Freight & Logistics
Driven by better fuel management and structural initiatives, company’s power and fuel costs have decreased 7% to INR1,262 per ton in Q3 FY ’25 from INR1,355 per ton in Q3 last year.
The share of green power in power mix has increased to 21.5% from 15.8%.
Ambuja Cements is focusing on three key strategies to reduce freight and logistics costs:
- Reduction in Lead Distance
- Target: Reduce lead distance by ~100 km.
- Progress:
- Primary lead distance: Improved to 265 km (vs. 268 km last quarter).
- Secondary lead distance: Reduced to 46 km (vs. 53 km).
- Drivers:
- Increased direct dispatch to customers (up 700 bps, from 50% to 57%).
- Network optimization (smarter routing, plant proximity adjustments).
- Warehouse Footprint Optimization
- Streamlining storage locations to minimize handling and transit costs.
- Rail-Road Mix Optimization
- Shifting more freight to cost-efficient rail transport (e.g., dedicated rakes for clinker/fly ash).
Impact: Logistics cost/ton declined 6% YoY to INR 1,239 (from INR 1,322).
Logistics Optimization & Cost Reduction Initiatives
1. Rail Transport Efficiency
- GPWIS Rakes:
- 11 rakes ordered and delivered, now operational in approved circuits.
- Purpose: Enable cost-efficient clinker movement from mother plants to grinding units.
2. Fly Ash Transportation
- BCFC Rakes:
- 26 rakes ordered for safe, low-cost fly ash transport from thermal plants.
- 5 rakes delivered and operational.
- 4 more expected by March 2025.
- 26 rakes ordered for safe, low-cost fly ash transport from thermal plants.
3. Cost Savings Achieved
- Logistics cost/ton reduced by 6% YoY to INR 1,239 (vs. INR 1,322 in Q3 FY24).
4. Raw Material Security
- Secured 2 new limestone mines (reserves: 631 million tons) in Madhya pradesh and Karnataka.
ESG & Sustainability Commitments
- Net Zero carbon goal by 2050. As a step closer to this goal, company recently partnered with Finland-based Coolbrook to implement its proprietary zero-carbon heating technology, cutting fossil fuel use in manufacturing.
- To promote the circular economy, company used waste-derived resources, like fly ash, slag and waste gypsum to substitute mineral resources.
- The company also used alternate fuels, such as municipal, industrial, agricultural, and plastic wastes, to replace fossil fuels.
- In Q3, the company used 4.8 million tons of waste-derived resources, which otherwise would have been dumped into the environment.
- In the last quarter, the company created societal values for more than 4.75 million people by contributing to fields like health care, education, employment and sustainable livelihoods.
- The company continues to partner with global national agencies like UNGC, WEF, AFID, GCCA, BEE, etc., to further advance our journey towards sustainable and responsible business practices.
Industry Outlook Summary
- Demand Recovery: Cement demand growth is expected to rebound to 4-5% in FY25, up from a sluggish 1.5-2% in H1 FY25.
- Key Growth Drivers:
- Stronger housing demand
- Increased infrastructure spending
- Pro-infra and pro-housing government budgets in 2025
- H2 FY25 Outlook:
- Demand anticipated to improve significantly compared to H1.
- Supported by government initiatives and seasonal construction activity.
Key Takeaways from CFO Vinod Bahety’s Commentary
1. Growth Strategy & Capacity Expansion
- Transition to Organic Growth: After 27 months of acquisition-led growth (post-Holcim stake purchase in Sep ’22), organic expansion will drive future growth starting March 2025.
- Capacity Targets:
- 100+ million tons by March 2025 (Q4).
- 118 million tons by FY26.
- 140 million tons by FY28.
- New Capacities: 45-50% of current base will be highly efficient (lower capex/opex, green power, rail infrastructure).
2. Cost Leadership & Operational Efficiency
- Cost Reduction Target: INR 530/ton reduction to achieve INR 3,650/ton by FY28.
- Renewable Energy:
- 200 MW solar commissioned (Dec ’24); 1,000 MW RE target by June 2026.
- Digitization:
- Cement Network Operating Centre (CNOC) in Ahmedabad optimizing “quarry-to-lorry” value chain.
3. Strong Financial Position
- Net Worth: INR 63,000 crores (up INR 12,000 crores since April 2023).
- Zero Debt: Maintained AAA rating with 15% of net worth as cash reserves.
- Tangible Assets: 75% of net worth backed by physical assets.