The global semiconductor landscape is shifting, with higher import duties—particularly from the U.S. targeting Chinese semiconductors—making headlines in 2025. For India, a nation heavily reliant on semiconductor imports, such changes might seem alarming at first glance. However, local players in India’s nascent semiconductor industry are poised to weather this storm and even thrive. From robust government support to strategic industry shifts, here’s why India’s semiconductor ecosystem remains resilient.
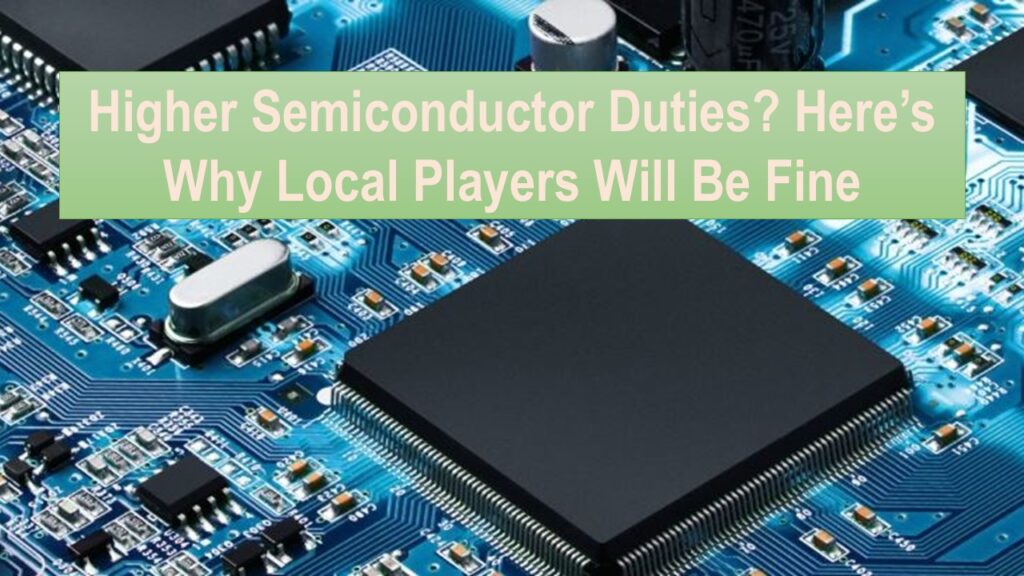
What Higher Semiconductor Duties Mean for India
Higher semiconductor duties refer to increased tariffs imposed by countries like the U.S. on imported chips, especially from China, which currently dominates global supply chains. In India, where 100% of semiconductor needs are met through imports (valued at approximately USD 52 billion in 2024-25, per the India Electronics and Semiconductor Association), this could theoretically raise costs for electronics and automotive manufacturers. However, the impact on India’s local players is cushioned by several key factors.
Why India’s Local Semiconductor Players Will Thrive
1. Government Backing: The Semiconductor Mission
India’s government has taken bold steps to reduce import dependency and build a self-reliant semiconductor ecosystem. The India Semiconductor Mission (ISM), launched in 2021 with a USD 10 billion outlay, offers incentives like 50% fiscal support for setting up fabrication units (fabs) and Assembly, Testing, Marking, and Packaging (ATMP) facilities. With projects worth over INR 1.5 trillion already approved—including Tata Electronics’ fab in Gujarat with Taiwan’s PSMC—local production is ramping up. These initiatives ensure that Indian firms aren’t solely reliant on costlier imports affected by duties.
2. Growing Domestic Market Demand
India’s semiconductor market is projected to grow at a 13% CAGR, reaching USD 103.4 billion by 2030 (IESA). Key sectors like mobile handsets (India is the second-largest 5G smartphone market globally), IT, and automotive drive this demand. Local players, such as Kaynes Technology and Micron’s upcoming ATMP facility in Gujarat, are aligning production to meet this domestic need, reducing exposure to global tariff fluctuations.
3. Diversified Supply Chains
Unlike earlier decades, Indian companies are diversifying away from China-centric supply chains. Imports from Vietnam, Thailand, and Malaysia already outpace China in some categories (Observatory of Economic Complexity, 2023 data). Partnerships with global leaders like Taiwan’s PSMC and U.S.-based Applied Materials (establishing an engineering center in Bengaluru) further bolster this shift, shielding local firms from tariff-induced disruptions.
4. Focus on Design and Innovation
India boasts 20% of the world’s semiconductor design talent, with over 100,000 engineers driving innovation. Companies like Tata Elxsi and HCL Technologies leverage this strength, contributing to global chip design while supporting local manufacturing. The Design Linked Incentive (DLI) scheme, offering up to INR 300 million for deployment, ensures that Indian firms remain competitive in high-value segments, unaffected by import duties.
5. Limited Export Exposure
As Ashok Chandak, President of IESA, noted in early 2025, “Tariffs are unlikely to impact India in the short term, as India is not a major semiconductor exporter to the U.S.” With exports forming a small fraction of the industry (USD 0.21 billion in 2017 vs. USD 4.65 billion in imports), local players face minimal direct pressure from U.S. tariffs, allowing them to focus on domestic growth.
Key Players Leading the Charge
- Tata Electronics: With fabs in Gujarat and Assam, Tata is set to produce 28nm chips by 2026, targeting automotive and AI applications.
- Kaynes Technology: Building an OSAT facility in Telangana with a capacity of 6 million chips daily.
- Micron Technology: Its Gujarat ATMP plant, operational by early 2025, will bolster local supply chains.
- Polymatech Electronics: Advocating for tax holidays and duty exemptions to attract further investment.
These companies exemplify India’s push toward self-sufficiency, supported by policies like the Production Linked Incentive (PLI) scheme, which offers 4-6% incentives on incremental sales.
Challenges to Watch
While the outlook is positive, challenges remain. Infrastructure gaps—reliable power, high-purity water, and logistics—could slow fab development. High upfront costs for advanced fabs also pose hurdles, though government subsidies mitigate this. Regulatory shifts, like potential changes to import duties on components, could temporarily affect costs, but long-term stratégies are in place to address these.
Conclusion
Higher semiconductor duties may ripple across global markets, but India’s local players are well-equipped to adapt. With government support via the ISM and PLI, a booming domestic market, and a pivot to diversified supply chains, the Indian semiconductor industry is on a growth trajectory. As the nation aims for a 10% share of the USD 1 trillion global market by 2030, local firms are not just surviving—they’re setting the stage to lead. For investors and stakeholders, India’s semiconductor story is one of resilience and opportunity.